Cores
Composite structures are usually designed to withstand forces in the x and y directions, with the fibre reinforcements being arranged accordingly. However, when a force is applied in the z direction, i.e. perpendicular to the surface, the fibres have little ability to resist it.

To address this problem, a sandwich structure is commonly used, which consists of two face sheets of traditional composite laminates, a core, and adhesive materials to hold the structure together. The primary function of the core is to increase stiffness and flexural strength and reduce warping of the laminate by effectively ‘thickening’ it. This can provide a dramatic increase in stiffness for very little additional weight. Thermal conductivity, sound insulation, and fire resistance can also be improved by use of the proper core material.
Bonded sandwich structures have been a basic component of the composites industry for over 45 years. The concept of using relatively thin, strong face sheets bonded to thicker, lightweight core materials has allowed the industry to build strong, stiff, light and highly durable structures that otherwise would not be practical. This technology has been demonstrated in boats, trucks, automobiles, wind turbine blades and building panels. A 3% weight increase can increase the flexural strength and stiffness by a magnitude of 3.5 times and 7 times respectively if cores and skins are properly chosen.
There are a number of types of core materials available, with a wide range of properties and costs:

3D Glass or else three-dimensional fiberglass fabric is a three-dimensional form of woven rovings, used for simple and quick production of sandwich constructions. Excellent mechanical performance and ease of use, makes it an ideal material for composite structures in the industry.
PVC foams came into use as core materials in the 70's. As sandwich structures in marine applications began to be optimized, a need for a low-density, consistent, moisture resistant core material was realized. Formulations were refined over the years and the characteristics of PVC foams fit the needs of the marine industry well. PVC foams are closed-cell, moisture resistant, and have good physical properties when compared to other foams of similar density.

PET Foam offers excellent thermal stability and low absorption. It also has good flame, smoke & toxicity properties, making it suitable for many transportation, military, and marine applications.

Polyurethane is available either in sheet stock form or it can be foamed in place when used as an insulation or buoyancy material. Polyurethane foam can be blown in a wide range of densities, from 2 lb/ft2 to over 20 lb/ft2. Because of its relatively low shear values, this foam is generally not used in structural applications.

PVC Foams are available in a variety of densities from 3pcf to 25 pcf (45kg/m3 to 400kg/m3). PVC foams can be formulated in rigid or ductile versions. Rigid PVC foams, sometimes referred to as crosslinked, have higher heat and solvent resistance than ductile foams. In addition, the physical properties are generally 20-40% higher. Shear strain to failure for rigid PVC foams varies with density between 12-30%. Ductile PVC foams, sometimes referred to as linear, have higher shear elongation to break, typically in excess of 40%. However, ductile foams have lower physical properties, heat and solvent resistance for a given density. PVC foam is closed-cell and has very low moisture absorption. It is self-extinguishing and will not rot. Other inherent properties are excellent fatigue life and good bond strength with common adhesives and resins.

Various types of manufactured honeycomb cores are used extensively in the aerospace and transportation industry. Honeycomb materials include paper, aluminium, phenolic resin impregnated fiberglass, polypropylene, and aramid fibre phenolic-treated paper. Densities range from 1 to 6 lbs/ft2. The physical properties vary to a large degree with the specific material and density. Fabrication of extremely lightweight panels is possible with honeycomb cores.

Nomex® honeycomb is made from Nomex® paper - a form of paper based on Kevlar, rather than cellulose fibres. It is widely used for lightweight interior panels for aircraft in conjunction with phenolic resins in the skins. Special grades for use in fire retardant applications (eg public transport interiors) can also be made which have the honeycomb cells filled with phenolic foam for added bond area and insulation. Nomex® honeycomb is becoming increasingly used in high-performance non-aerospace components due to its high mechanical properties, low density and good long-term stability. However, it is considerably more expensive than other core materials.
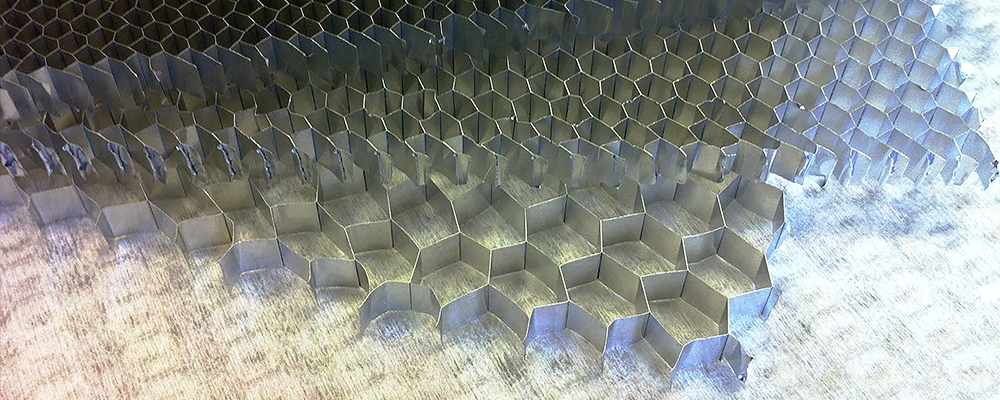
Aluminium honeycombis one of the most widely used high performance honeycomb materials; chosen for its excellent strength to weight ratio (the best of all core materials) and bonding characteristics. Aluminium honeycomb is used extensively in the motorsport, marine and aerospace industries and increasing now in construction industry where reducing weight whilst maintaining or improving the strength of a composite is of key importance.

Phenolic honeycomb is a high performance non-metallic core, available in a wide range of densities, suitable for most composite sandwich applications. It can be readily heat formed to help produce complex components and offers excellent thermal stability and low moisture pickup.
Contact us to discuss your project with one of our experts in the field.