Epoxy Resins
Epoxy resins have a well-established record in a wide range of composites parts as well as in concrete repair. Epoxies are used primarily for fabricating high-performance composites with superior mechanical properties, resistance to corrosive liquids and environments, superior electrical properties, good performance at elevated temperatures, good adhesion to a substrate, or a combination of these benefits. Surfaces of epoxy resin composites are not cosmetically appealing, so the material is a good choice in applications where functional requirements outweigh aesthetic ones.
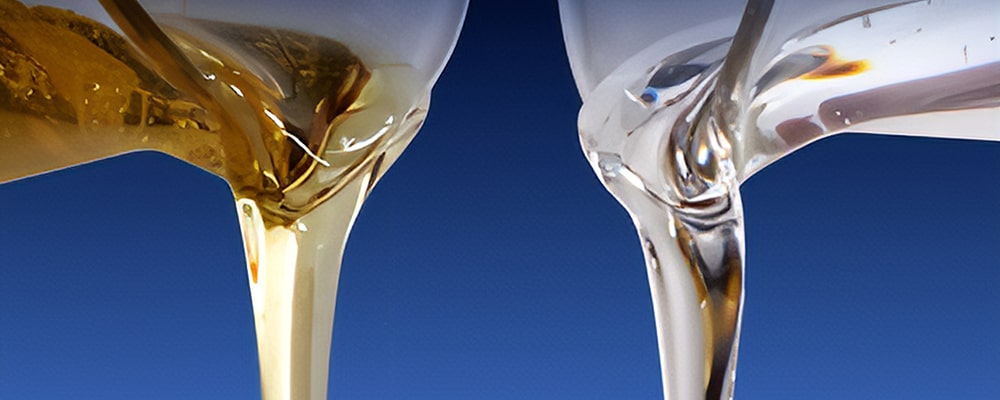
It can be used in applications ranging from sleek automotive body panels to rugged floor or wall panels. It is particularly well suited to kitchens, bathrooms, and other areas that require washable low-maintenance walls. Its low density makes it up to five times lighter than equivalent metal parts and its strength to weight ratio is very good.
The composite’s strength can be increased or decreased by altering the proportion of reinforcement. Fillers may also be added to extend the value of the resin, reducing the cost of the final composite by as much as 50 percent.
The structure of the resin can be engineered to yield a number of different construction products with varying levels of performance. A major benefit of epoxy resins over polyester resins is their reduced shrinkage upon curing. Epoxy resins can also be formulated with different materials or blended with other epoxy resins to achieve specific performance features.
Advantages
- Outstanding electrical insulation
- High temperature and chemical resistance
- Excellent adhesion to reinforcements
- Extremely low shrinkage
- Almost no odour
Limitations
- Cost of epoxy resins is approximately three times as much as that of polyester resins
- Epoxy resins do not have particularly good UV resistance
- Since the viscosity of epoxy is much higher than that of most polyester resins, a post-cure (elevated-heat) process is often required to obtain ultimate mechanical properties
- Epoxies do not produce cosmetically appealing finishes, so they are best used in applications where functional requirements outweigh aesthetic ones
Processing technologies
Epoxies are compatible with most composites manufacturing processes particularly:
- Vacuum bagging
- Compression moulding
- Hand lay up
BFG International’s experienced designers and engineers select the optimal process in each case based on variables such as the client’s tooling budget, dimensional tolerance and physical properties of the parts, and production volume.
Techinical details | |
---|---|
Maximum use temperature | 93 – 177 °C |
Flexural strength | 45 – 44 ksi |
Flexural modulus | 2.0 – 2.4 Msi |
Tensile strength | 5 – 15 ksi |
Tensile modulus | 0.6 – 0.7 Msi |
Density | 1.2 – 1.25 grams/cc |
Moisture absorption | 0.1 – 0.6 % |
Elongation | None |
Coefficient of thermal expansion (x10-5) | 6 – 7 |