Open vs Closed Moulding
BFG International employs a variety of composites manufacturing technologies which can be used to produce large quantities of uniform products or a single one-time moulded part. Our experienced engineers will select the best method for your project based on factors such as production volume, parts dimensions, budget, and other requirements.
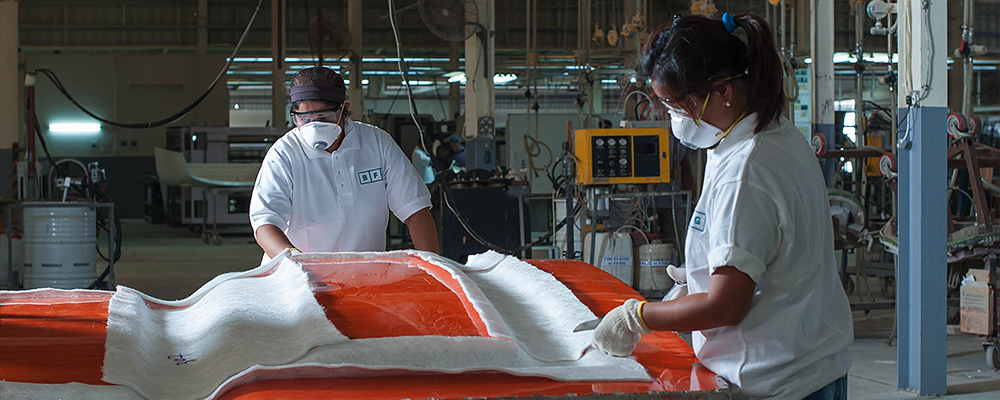
The difference between open moulding and closed moulding is in how the resin is cured. When the resin is exposed to the atmosphere during the cure, it is referred to as open moulding. When the resin is not exposed to the atmosphere during cure, it is referred to as closed moulding.
Open moulding
Tooling cost for open moulds is relatively low, making it possible to use this technique for short production runs.
Typically, the open moulding process is used for a large size range of products that cannot be produced in more automated processes, or for parts that are produced in low volumes that cannot justify the higher mould costs of automated processes.
Open moulding methods employed at BFG International include:
- Contact moulding (hand lay up)
- Spray up
Closed moulding
Closed moulding is used to produce large quantities of precision parts or in situations when an aesthetic finish is required on both sides of the part.
Closed-moulding processes are usually automated and require special equipment. In closed moulding, dry reinforcements are laid into the base mould, the mould is closed and resin is introduced into the closed cavity using a pressure pump or vacuum. When the laminate is cured the mould is opened and the part removed.
Advantages of closed moulding include lower material and disposal costs; a more consistent, repeatable process; and reduced cycle times, which leads to higher productivity and lower labour costs. Since the resin is cured in a closed mould system, it also results in lower emissions and reduced waste.
Closed moulding methods employed at BFG International include:
- Light RTM
- Heavy RTM
- Vacuum infusion
- Vacuum bagging
- Press moulding
- SMC
- Vacuum forming